Industry: Semiconductor
Process: Copper recovery from concentrated wastewater streams for discharge compliance
Benefits:
- Eliminate associated hazardous waste hauling risk & cost
- Reduce CO₂ emissions from inbound & outbound heavy trucks
- Operating revenue from recovered copper
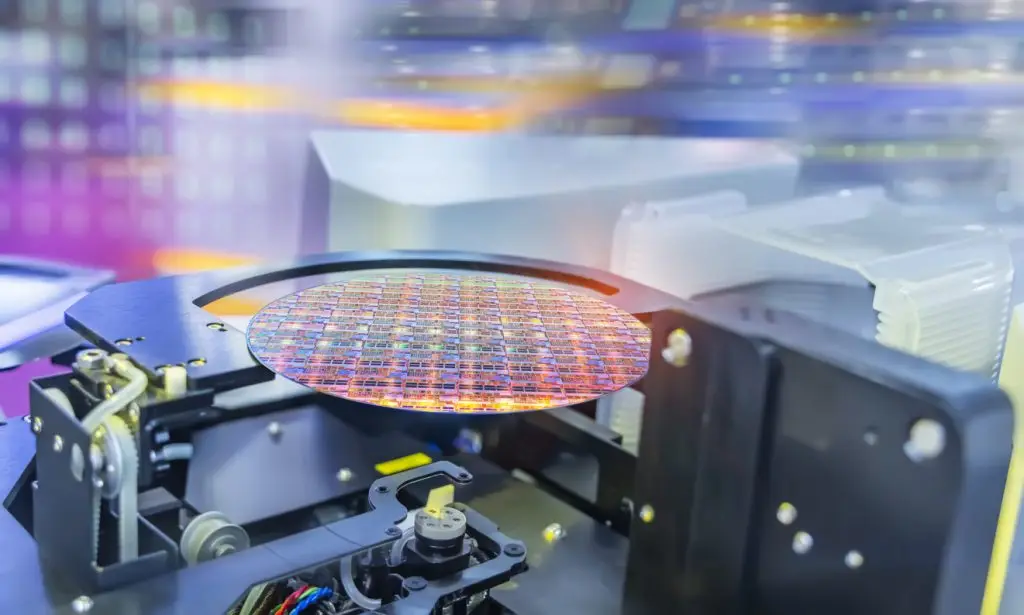
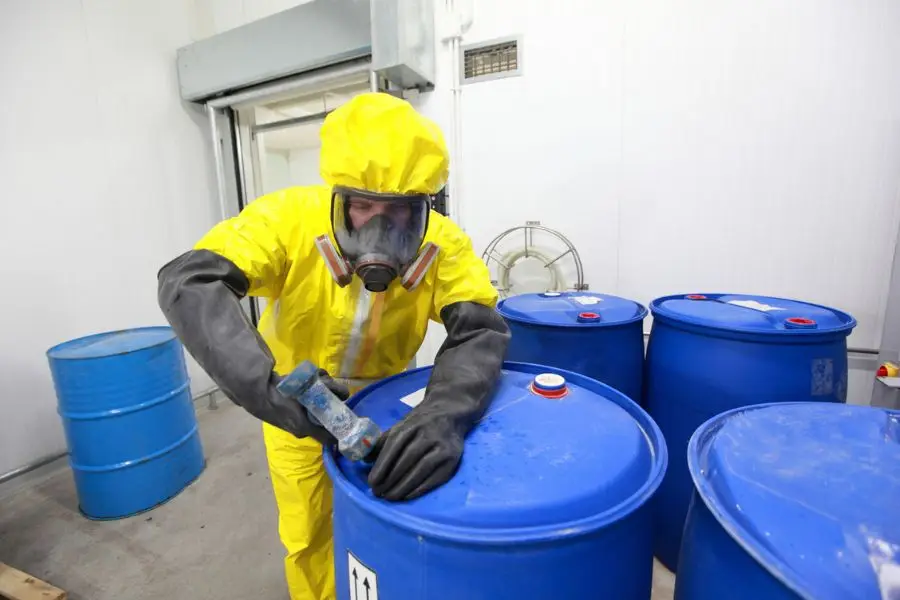
Background
The semiconductor industry is undergoing a surge of unprecedented growth fueled by the demand for electrification of our society. From electric vehicles to renewable energy solutions, the thirst for chips is unquenchable. Behind the curtain of this remarkable expansion, there’s a significant challenge related to water stress and a continuous search for operating budget optimization. Necessary process chemicals like sulfuric acid and hydrogen peroxide are typical and generate copious amounts of hazardous waste. Plating and test wafer regen waste streams are especially challenging due to high levels of copper, sulfuric acid, and hydrogen peroxide. Due to the complex nature of this wastewater, the traditional solutions are to (a) ship it offsite for 3rd party processing and disposal or (b) treat it with very expensive traditional electrowinning equipment. Due to high capital costs, peroxide treatment challenges, and low return on invested capital, most fabs have turned to hauling the waste offsite. This offsite treatment eliminates opportunities for both acid and water recovery and reuse.
Challenges
A semiconductor facility produced ~15,400 Liters daily of concentrated copper wastewater (11,200 mg/L) that was collected and hauled off-site for disposal. The annual cost for offsite treatment exceeded $3,000,000 and resulted in an unrealized copper recovery of ~$0.5M. The hauling process introduced operating risk during adverse events while the daily trucking presented avoidable risk to the community and environment. Operating costs and risks justified investigation into a better solution. Recovery of the sulfuric solution with peroxide and copper removed presented a tertiary value proposition allowing reuse in the cooling tower system to avoid buying new technical grade sulfuric acid.
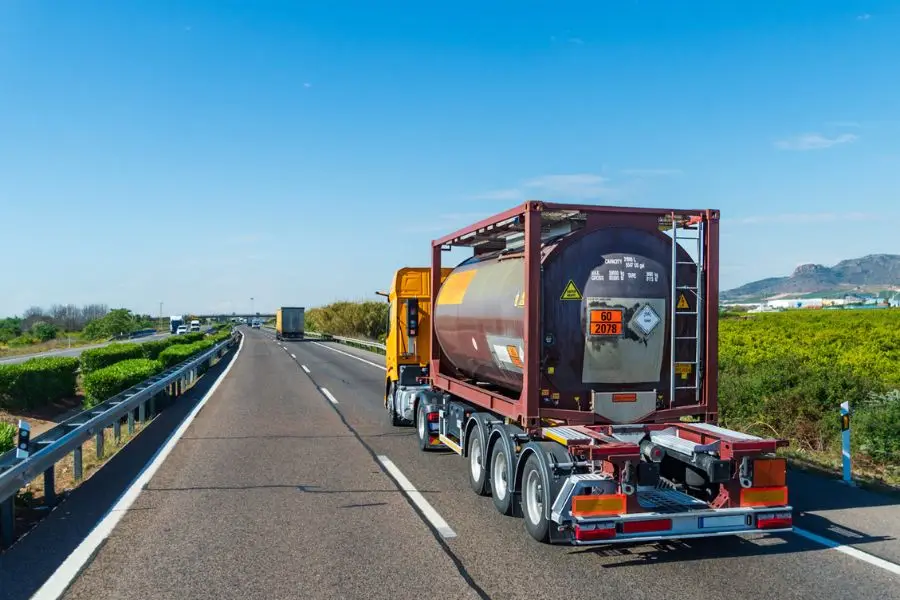
Challenge
High [H₂O₂] & [Cu] created treatment feasibility issues
Electrowinning + IX return on invested capital (ROIC) was unfavorable
Storage and Hauling Challenges presented economic advantages but higher risk
Lost circularity opportunity for copper
Lost circularity opportunity for acid solution
Solution
Cost-effective Cu recovery also enabled acid-water reuse
Lower capital combined with higher grade copper exceed ROIC
Onsite recovery eliminated hauling risks and costs
Abatement of H2O2 enabled Cu recovery & sales
Removal & Recovery of Cu enables Reuse in Cooling Towers
Impact
ElectraMet Gamma & Alpha Systems enabled treatment with acid & copper recovery
9.2-month return on invested capital
Eliminated $3.2M in associated hauling fees & reduced annual burdened labor by 706 hours
ElectraMet Gamma enabled copper recovery ($499,550)
ElectraMet Alpha systems enabled 6.1M liters in acid-water recovery
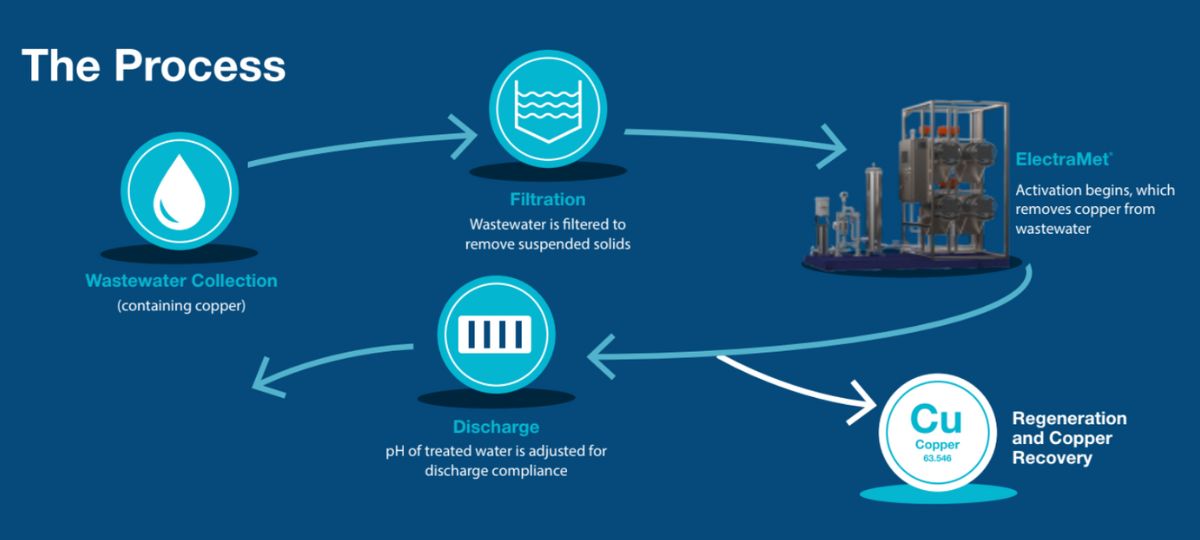
Proven Results | Case Study
Fab expectation was exceeded with a mean copper effluent at 0.72 mg/L and +/- 0.17 effluent variability. This was achieved with 32 bulk recovery cartridges, 16 coarse removal cartridges, and 4 fine removal cartridges with current efficiency >90%. The system footprint totaled 59.2 m2 with location in the industrial treatment building due to low ceiling height (optimized footprint was possible at 36.2 m2).
Onsite recovery of pure copper tubes enabled circularity of the copper and reuse of the acidic water for cooling tower makeup. When combined with a reduction in burdened labor, the copper recovery, acid/water reuse, and labor savings exceeded $0.66M. Hauling fees were reduced by $3.2M and water reclamation totaled 6.11M liters.
ElectraMet’s automated electrochemical process selectively removes and recovers Cu from complex process water or wastewater streams. The system is modular and can scale as production grows. The system consumes very little power of <0.5 kWh/m3 treated with observed current efficiencies >90%. ElectraMet uses three cartridge types to remove and recover copper from concentrated waste streams. Details on treatment and removal rates are shown below.
Copper Removal & Recovery
Cartridge Type | Treatment Ranges | Daily Removal Rate | Current Efficiency |
---|---|---|---|
Bulk Recovery | >200,000 ppm to 3,000 ppm | 8.11 kg/cartridge | 99% to 95% |
Coarse Removal | 3,000 ppm to 100 ppm | 5.86 kg/cartridge | 99% to 95% |
Fine Removal | 100 ppm to <10 ppb | 0.82 kg/cartridge | 99% to 38% |
ElectraMet’s process enables metal and water circularity, reducing costs while ensuring up time. This economic and environmental solution is a winning combination, benefiting the plant, its employees, and the surrounding community.