Situation
Hydrogen peroxide is crucial in microelectronics manufacturing where it serves as a powerful oxidizing agent for cleaning, etching, and surface treatment processes. Its primary function is to remove organic contaminants and metal oxide layers from semiconductor, electronics pieces, and other surfaces, which makes it vital for fabrication processes. Significant quantities of hydrogen peroxide-containing wastewater are generated that are often contaminated with organic residues, heavy metals, and other impurities. This wastewater poses a risk to downstream processing and treatment equipment as well as the environment if discharged. Various methods of H2O2 destruction are available, with catalase and Fenton chemistry being the most prevalent, but they come with significant drawbacks and burdens to the production facility.
The Challenge
A semiconductor facility’s wastewater stream had elevated H2O2 values up to 16,000 ppm. The site experienced significant challenges using catalase (“liquid gold”) to breakdown the H2O2 and enable consistent water reuse. The high concentration of H2O2 required significant dosing of catalase, resulting in high annual operating costs, while the presence of enzyme in the stream promoted biofouling, requiring unplanned downtime and labor to remediate. The facility initially explored carbon-beds to remove the H2O2, but the beds were not effective over 400 ppm while also introducing fouling concerns. Fenton chemistry was considered, but the high chemical usage for the stoichiometric reaction and resulting sludge generation were unfavorable to building a cost-effective and sustainable operation.
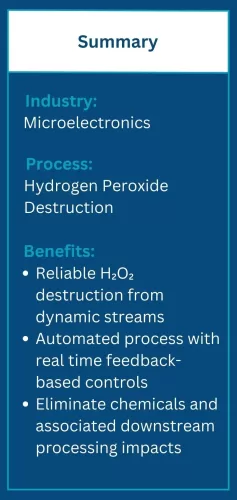
ElectraMet’s solution uses a redox-active media to catalytically break down the hydrogen peroxide from process water and wastewater streams. ElectraMet’s chemical-free process is a circular solution for handling H2O2 in process & waste streams, which benefits the plant, its employees, the surrounding community, and the environment. Post-commissioning, the only byproducts impacting the stream will be water (H2O) and oxygen (O2).
Additional observed benefits include:
(1) Reduced operator hours due to reliable catalytic destruction
(2) Increased personnel time spent on preventative maintenance for other systems
(3) Improved downstream processing performance due to low H2O2 effluent quality
ElectraMet’s Gamma™ system incorporates this catalytic media into reaction chambers with modulated flow and monitoring to ensure specification is attained. The flow modulation enables resonance time for the media to execute the two-step destruction process and regenerate itself while in service. No chemistry or additives are required for H2O2 or media regeneration. Expected lifetime of the media is five years pending feed specification adherence.
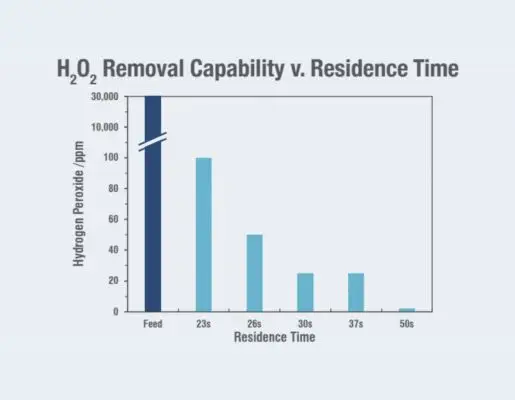
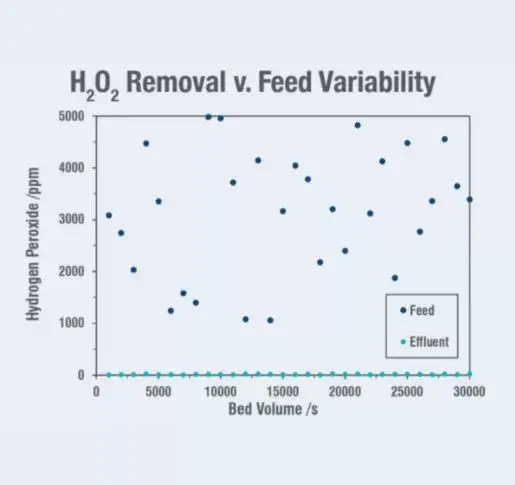
Proven Results | Case Study
The process waters of a semiconductor facility contained elevated levels of H2O2 of up to 5,000 ppm with varying amounts of organic compounds and dissolved copper. The site needed to remove the H2O2 to < 10 ppm for downstream processes to function properly and effectively. ElectraMet’s (Redox-Active) media solution was implemented to:
(a) Replace costly chemical consumables
(b) Ensure effluent quality
(c) Enable reliable downstream processing operations
Site specifications were achieved through the rapid destruction of > 99.9% of the H2O2 in a single pass through the redox-active media, which reduced the downstream labor requirements. Required residence time was achieved through the Gamma™ system while maintaining standard flow rates for the fabrication effluent stream. Over 2 years of operation, the site was able to:
•Reduce their annual operating costs by > 35% for H2O2 treatment by eliminating catalase consumable
•Eliminate downstream fouling while increasing reuse efficiency
•Maintain 100% planned equipment up time for process