Background
The global drive for autonomous battery-powered electronics and vehicles is growing rapidly, translating to increased waste associated with Lithium-ion (Li-ion) batteries. Currently, end-of-life batteries are shredded and processed to form a black mass, containing high amounts of lithium, manganese, cobalt, and nickel. Reuse of these metals for the production of new electric vehicle (EV) batteries alleviates the need for mining new materials which have significant negative environmental impacts.
Challenges
Impurity removal of black mass leachate is a complicated part of the EV battery recycling process, critical to achieving high purity metal salts for manufacturing cathode active materials (CAM). Traditional treatment methods such as chemical coagulation or ion exchange are inefficient and struggle to meet purity specifications required due to the complex nature of the water matrix which contains large amounts of interfering metals. Identifying a process to reduce impurities in the refining stages is imperative to provide a scalable and profitable outcome.
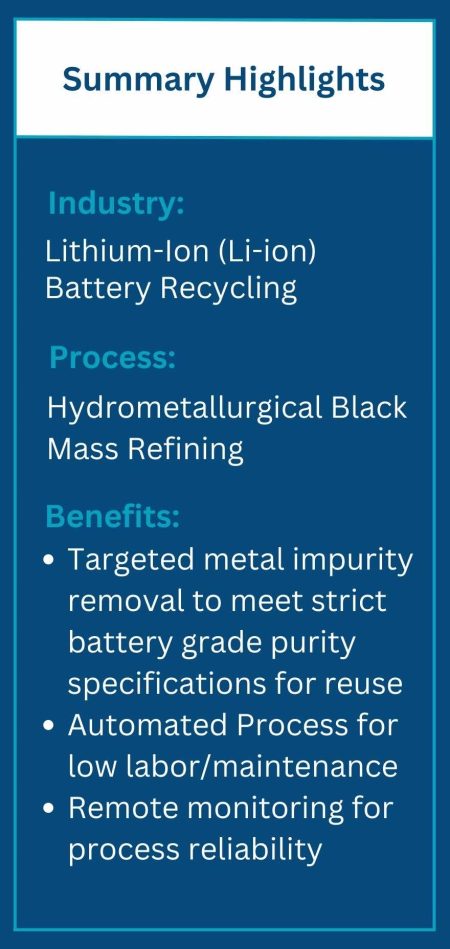
Proven Results | Case Study
The black mass leachate at an EV battery recycler facility is processed via a hydrometallurgical process. Each step of the process contains trace metal impurities that need to be removed to < 2 ppm to meet strict battery-grade purity specifications. Their traditional treatment solutions solvent exchange and chemical precipitation were not removing the trace metals to meet purity specifications. ElectraMet’s modular solution was retrofitted into their existing process to deliver:
Steps:
- Copper impurity reduced to < 0.5 ppm
- manganese impurity reduced to < 0.41 ppm
- Nickel & Cobalt impurity reduced to < 0.5 ppm
The site was able to:
- Maintain 100% planned process uptime
- Produce battery-grade metal salts suitable for CAM production that meet strict purity specifications
- Increased yield of metal products
Observed benefits include:
- Reduced operator hours due to automation and adjustments
- Produce Reduced man hours associated with chemical additions and grab sampling
- Analytics-informed troubleshooting maximized uptime & production quality
- Increased personnel time spent on preventative maintenance for other systems
ElectraMet’s automated process uses an electrochemical process to selectively remove targeted metals and impurities for EV battery recyclers. The system is modular and can be scaled and interfaced as production grows. The system uses very low amounts of energy. With its capture and recycling technology, ElectraMet’s chemical-free process presents a circular solution for handling copper and other trace metal impurities, benefitting the plant, its employees, the surrounding community, and the environment. With online system diagnostics for varied parameters, ElectraMet provides real-time feedback on performance, ensuring the process is working and lithium battery recyclers can concentrate on their core competencies.
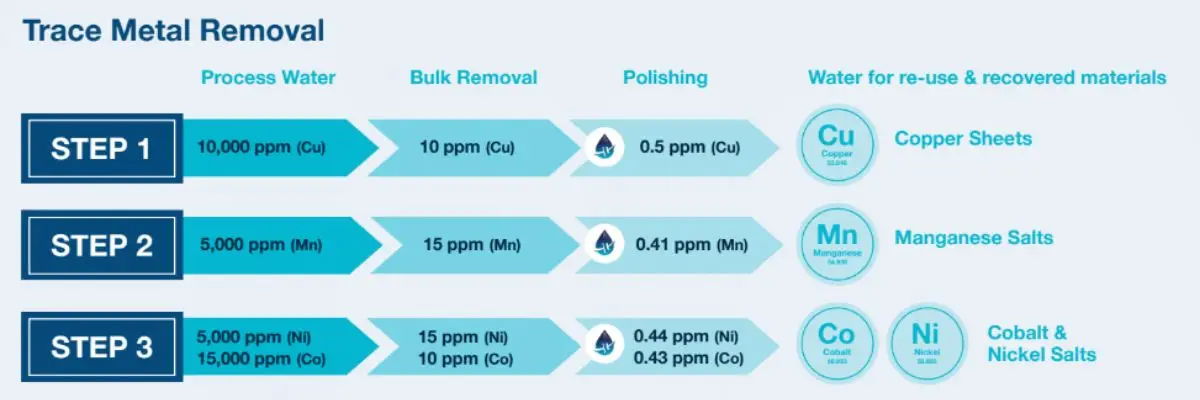