Industry: Aerospace, Aviation, and Defense
Process: Electroforming Process
Benefits:
- Bath life extension
- Improved production yields
- Reduced rework of defective parts
- Reduced wastewater sludge & disposal
- Assured discharge compliance assurance
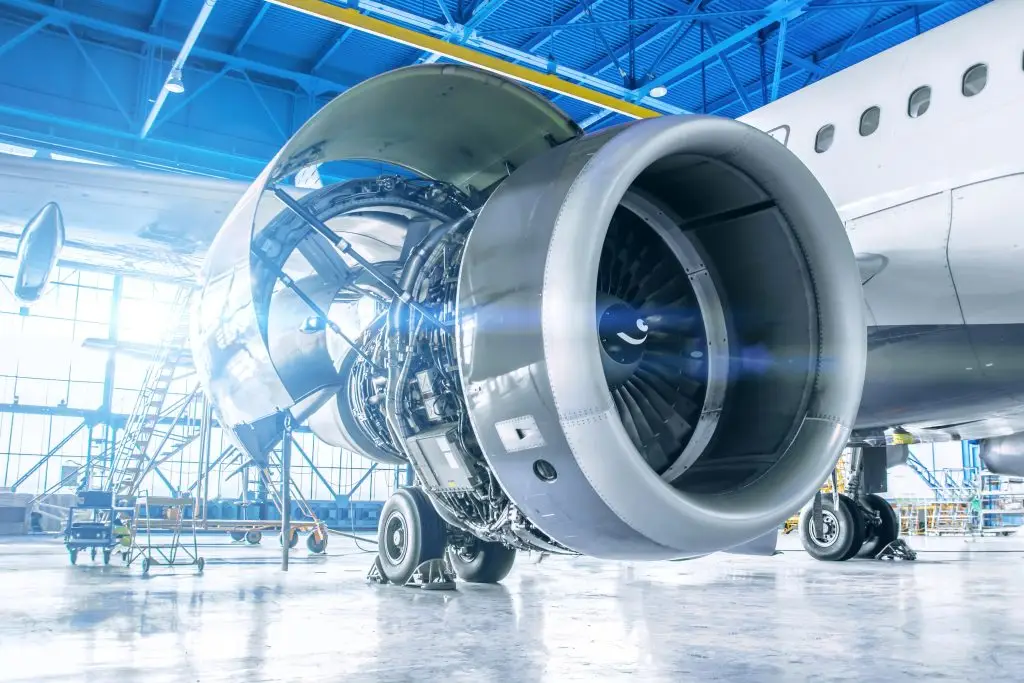
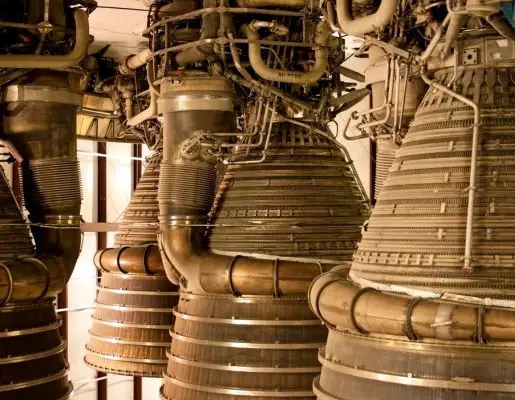
Background
Copper management plays a crucial role in the electroforming processes used within the aerospace, aviation, and defense industries. Electroforming enables the production of high-precision, lightweight parts with superior strength, corrosion resistance, and heat tolerance. Key metals, such as copper, nickel, and their alloys, are critical due to their electrical conductivity and ease of use in forming intricate parts. However, inconsistent copper concentrations in electroforming baths can lead to severe manufacturing defects, impacting part quality, performance, and production yield. These inconsistencies also result in premature bath exhaustion, increased waste disposal, and discharge compliance risks. All of this drives operating margin down for the manufacturer. As the demand for mission-critical components grows, maintaining tight process control over copper levels is essential to meet stringent quality standards and ensure operational efficiency.
Challenges
A leading aerospace and defense manufacturer faced significant challenges in managing copper concentration within their electroforming process.
The manufacturer aimed to:
(1) achieve consistent, high-quality electroformed components to meet tight tolerances and specifications;
(2) extend bath life to reduce costs related to virgin bath preparation and disposal; and:
(3) minimize wastewater treatment disruptions to ensure environmental compliance.
Previous manual approaches to bath testing and adjustment were labor-intensive, prone to human error, and inconsistent. High and low copper levels led to defective parts, rework, and increased operational costs. Unscheduled bath dumps further strained wastewater treatment systems, creating compliance risks and disposal expenses.
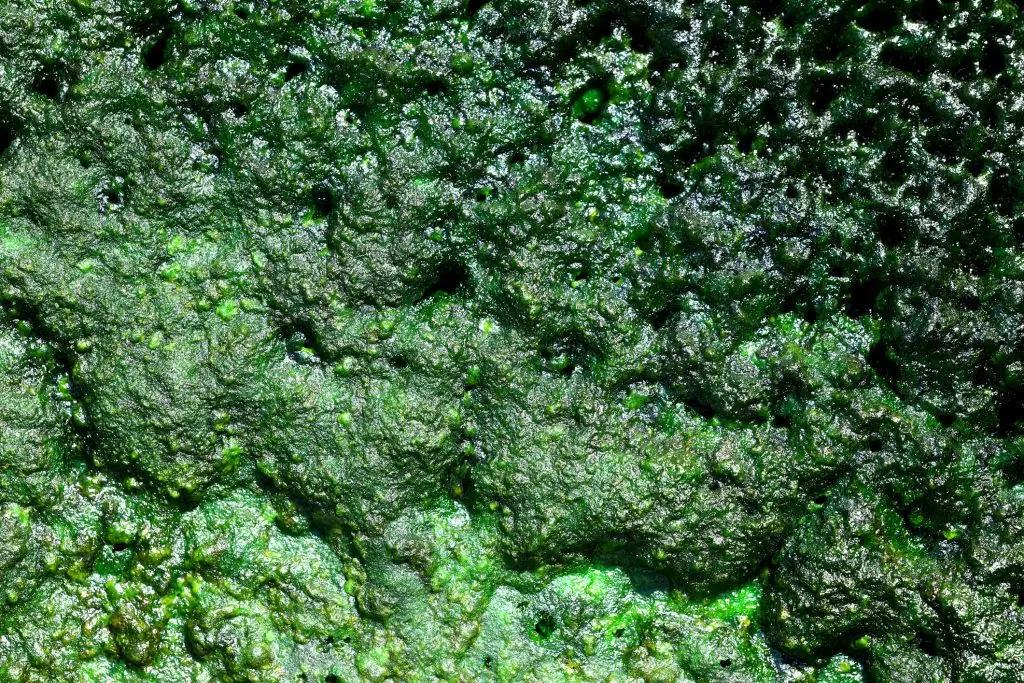
Challenge
Maintain consistent copper concentration in electroforming baths
Achieve greater than 90% first-pass part quality
Extend electroforming bath life & eliminate upsets to wastewater treatment
Solution
Continuous process control of copper concentration using an ElectraMet® Phi System
Maintained target mandrel surface preparation and deposition layer thickness
Automated bath impurity removal with real-time feedback
Impact
Saved >$310,000 annually on virgin bath preparation and makeup & reduced treatment/disposal expenses
Achieved >98% first-pass part quality & >$260,000 in annual rework costs eliminated
Eliminated labor and error-prone manual bath testing and adjustments
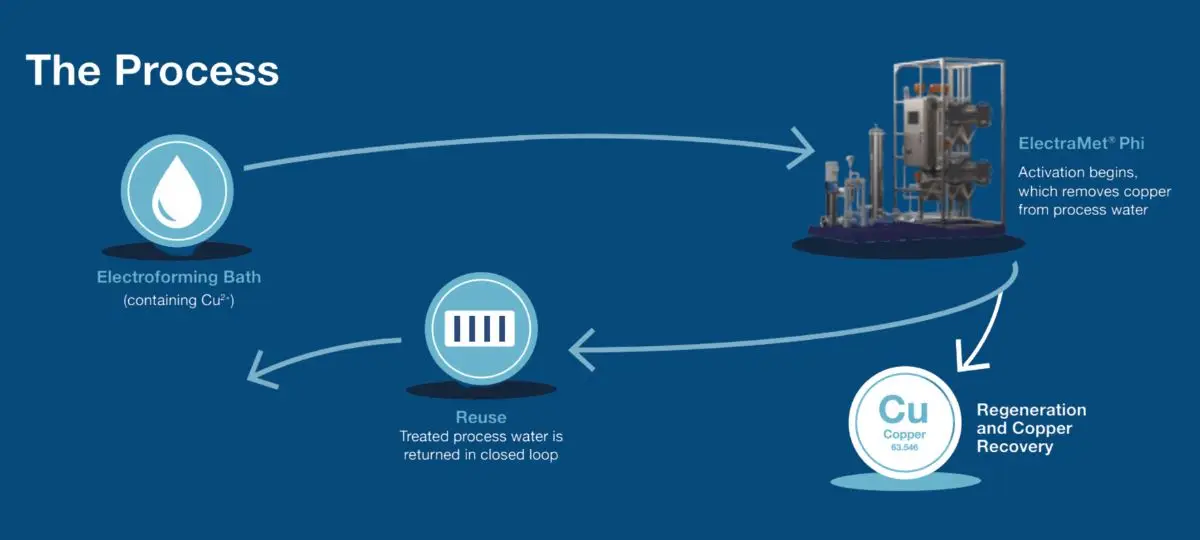
Proven Results | Case Study
A tier 1 aerospace and defense manufacturer employed an electroforming process utilizing a copper mandrel substrate to electroform a separate metal and create critical componentry. The company faced significant issues with inconsistent dissolved copper levels in their electroforming baths. Low concentrations compromised metal adhesion and accumulation to the mandrel, while high concentrations created over-deposition resulting in surface imperfections and out-of-tolerance rejection. Varying inconsistencies resulted in manufacturing defects, rework, and associated operational inefficiencies that threatened production timelines and product quality.
Although the bath properties were tested and adjusted manually several times a day, the process was prone to inconsistent results. When baths were deemed exhausted by manual testing, the baths were off-streamed into a wastewater system designed to handle the waste. While it delivered results, chemical usage, toxic sludge handling costs, and compliance risk was high.
An ElectraMet® Phi system was implemented to establish electroforming process control for copper concentrations. The process control is shown in FIGURE 1, allowing continuous copper concentration management to achieve a targeted bath level at 10-50 ppm. ElectraLink®, an onboard control software, provides process assurance in real-time. Based on this success, an ElectraMet® Phi system was installed to manage the copper waste stream onsite, maintaining discharge compliance despite variable feed concentrations (FIGURE 2).
ElectraMet’s automated solution delivered measurable impact:
- >98% first-pass part quality resulting in >$260,000 savings annually;
- >$310,000 annual savings for reduced bath preparation and disposal fees;
- improved wastewater treatment compliance, avoiding over $110,000 in chemical costs and $50,000 in sludge disposal annually; and
- reduced environmental risk with copper discharge consistently <1 ppm.
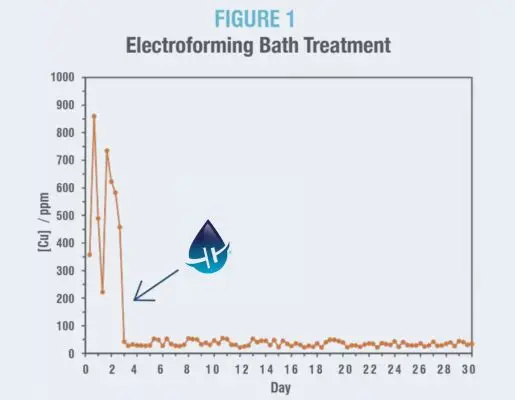
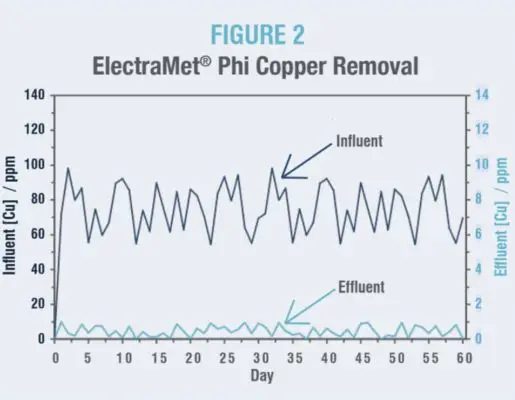