Background
Microelectronics manufacturing uses diverse raw materials, chemicals, and processes. As part of the production finishing process, chemistries diluted with deionized water (DI) are used to remove particles, residues, metallic impurities, and organic contamination from the sensitive components. While assuring quality and longevity for the manufactured components, this rinse results in wastewater treatment requiring unit processes to address the varied treatment and regulatory needs placed on the facility. The metals found in the rinse water must be treated and disposed of according to EPA and local regulatory guidelines. Chemistry is the traditional treatment method, which prevents recovery and produces various classifications of hazardous waste, requiring special handling and disposal.
Challenges
A global microelectronics manufacturer produces components for smart devices and tablets. As part of the production process, rinse steps are used as described above to remove debris and deliver high quality components. The local regulatory body was indicating that the discharge permit for Copper would be dropping, while the production forecast was increasing. The traditional chemical waste treatment method allowed the site to meet discharge compliance, but lower limits combined with increased production meant more chemistry and more sludge production. The current chemical solution required constant maintenance and regular jar testing to assure process control, the disposal cost of the chemically-produced sludge was high, while the value of recoverable copper was lost. While the EPA’s Common-Sense Initiative and Resource Recovery Act were created to help metals sludge producers manage recovery of metals, the economics and space requirements don’t typically favor onsite treatment and recovery of metal, until now
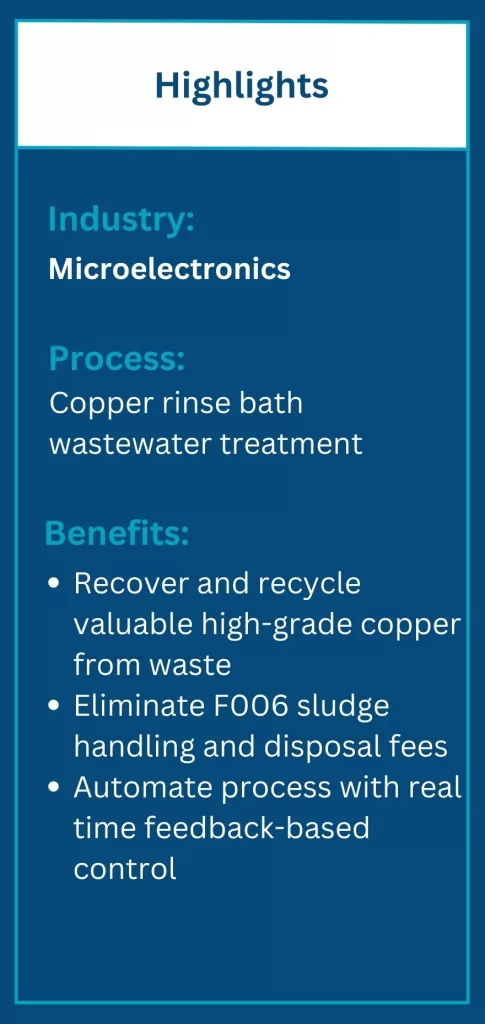
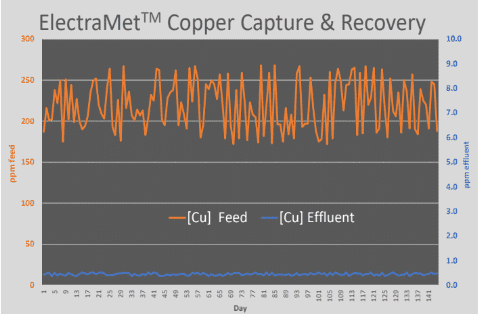
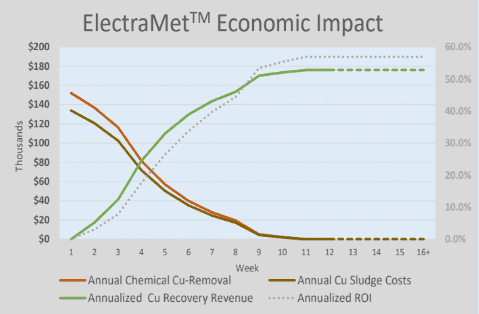
Proven Results | Case Study
The rinse bath waste stream generated at a microelectronics manufacturing facility contained 171 – 268 ppm of Copper (Cu), with a mean value of 221 ppm. The site permit allowed for 2.07 ppm in their discharge. Due to site expectations and an expectation of tightening regulations, the site selected 0.6 ppm (600 ppb) as the effluent target. ElectraMet’s modular solution was implemented in phases to control the changeover from chemistry at the customer’s request, resulting in a 12-week implementation and approval process.
Over a 12-week period, the site was able to:
- Eliminated chemical precipitation for Copper (-$152,000 annual)
- Eliminated Copper-based sludge disposal (-$134,000 annual)
- Produced recyclable Copper revenue (+$176,000 annual)
ElectraMet’s automated technology uses an electrochemical process to selectively remove targeted metals and impurities for microelectronics manufacturers. The system is modular and can be scaled and interfaced as production grows. The system uses very little electricity and was installed using existing electrical. With its capture and recycling technology, ElectraMet’s chemical-free process presents a circular solution for handling copper in waste streams, benefitting the plant, its employees, the surrounding community, and the environment.
Additional observed benefits include:
- Reduced operator hours due to automation and analytics which informed adjustments,
- Reduced man hours associated with collection, storage and movement of sludge,
- Analytics-informed upstream process troubleshooting maximized uptime and production quality, and
- Increased personnel time spent on preventative maintenance for other systems.