Background
Electropolishing of stainless steel is a highly effective method of improving surface finish and cleanliness. This transformative process involves immersing the material in an aqueous solution and applying an electrical current. However, during electropolishing, a small amount of chromium, which gives stainless steel its remarkable strength and corrosion resistance, is released as Cr(VI), which is classified as an RCRA element. Therefore, prior to discharge, proper remediation procedures must be followed to prevent negative environmental impacts.
Challenges
A large steel mill produces a variety of hot and cold-rolled stainless steel products, producing a wastewater stream containing elevated Cr(VI). Production for the mill was forecasted to increase, while the permitted Cr(VI) discharge limit was to be lowered. The planned change meant more chemistry and more variability in the waste stream. Typical to steel mills, the real-time availability of data associated with Cr(VI), the treatment process, and operational conditions was not available. The plant solution consisted of bisulfite chemistries, rated 4/4 for Acute Oral Toxicity and 3/4 for Specific Organ Toxicity. Despite aggressive chemistry and constant maintenance with regular sampling and jar testing to assure process control, Cr(VI) breakthroughs still occurred. The result was batch re-work before chemical precipitation, significantly increasing the total cost of compliance.
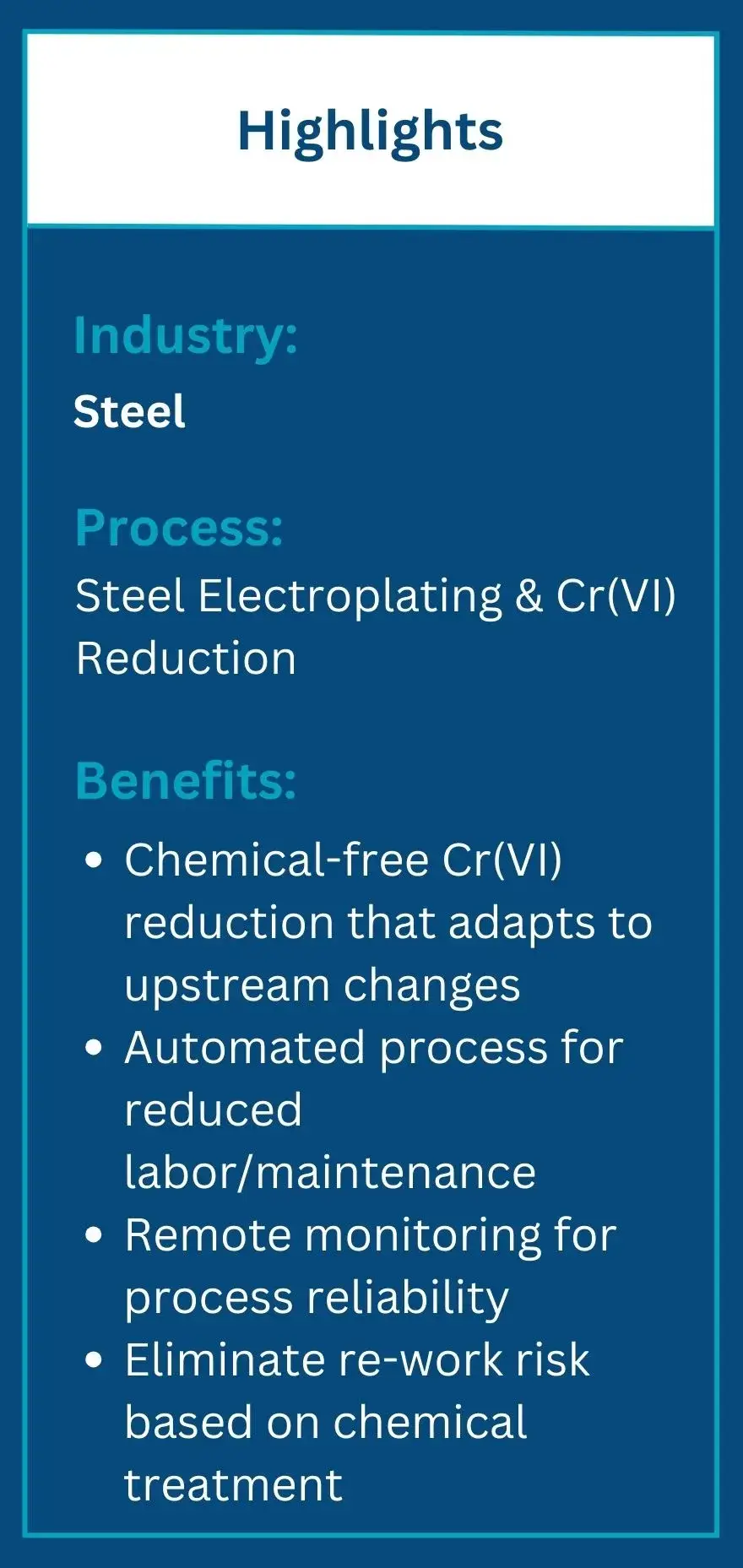
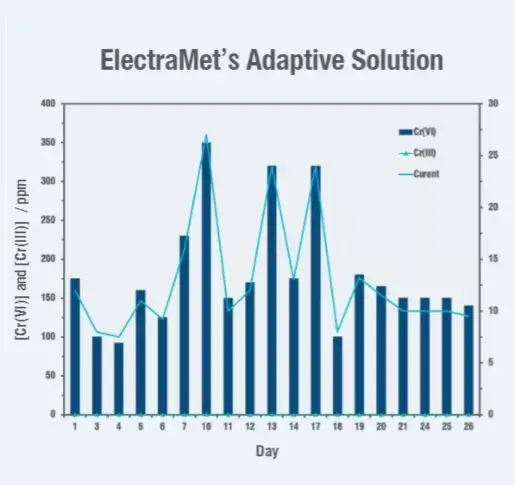
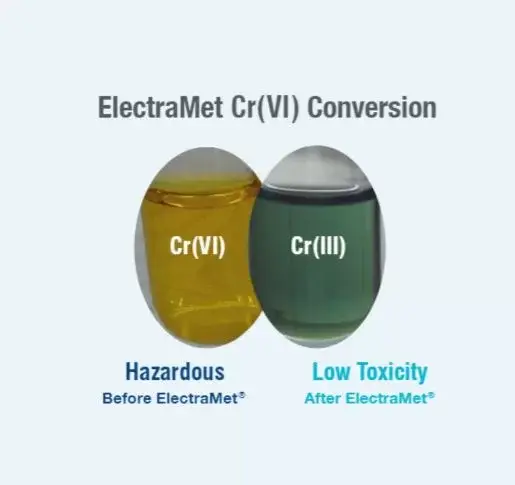
Proven Results | Case Study
The waste streams generated from electropolishing stainless steel at a steel plant contained variations from 100 ppm – 400 ppm Cr(VI). The site permit allowed for 0.2 ppm in effluent discharge. Due to site expectations and anticipated tightening regulations, the site selected 0.1 ppm (100 ppb) as the effluent target for ElectraMet to deliver.
ElectraMet’s automated solution uses an electrochemical process to selectively reduce the Cr(VI) to Cr(III), suitable for downstream removal via caustic precipitation as Cr2O3. The dynamic nature of the feed concentrations caused a large excess of chemicals to be used to ensure complete treatment. ElectraMet’s adaptive solution was able to treat this dynamic stream without operator input and with an average power consumption of 0.17 kWh/m3 treated. The effluent Cr(VI) levels were consistently below the 0.1 ppm threshold and produced a vibrant green color, confirming the complete reduction of Cr(VI).
The system is modular and can be scaled and interfaced as production grows. The system uses very low amounts of energy. With its capture and recycling technology, ElectraMet’s chemical-free process presents a circular solution for handling metal in waste streams, benefiting the plant, its employees, the surrounding community, and the environment.
Additional observed benefits include:
- eliminated >1 million pounds of annual chemical use,
- reduced operator hours due to automation and analytics which informed adjustments,
- analytics-informed upstream process troubleshooting maximized uptime and production quality, and
- Increased personnel time spent on preventative maintenance for other systems.