Background
Copper foil production uses high purity materials, chemicals, and processes to drive efficiency and repeatability. As part of the production, electrolytic plating and surface treatment processes are used, which generate large volumes of copper-laden wastewater. Traditional treatment processes like chemical coagulation with floc-tube reactors (dissolved air flotation, DAF) are time, footprint, and energy intensive while producing toxic sludge that must be trucked off to landfill. Significant labor is required to maintain these systems not typically included in the operations risk profile or the total cost of ownership.
Challenges
A copper foil production facility struggled with rising costs for chemistry and sludge handling as well as increased operational burdens with maintaining the DAF system. The site was producing 85 gpm of copper-laden wastewater containing ~1,800 ppm of copper. The process controls were visual inspection during plant walks and laboratory test with grab samples once per shift. Chemical coagulation systems with DAF lose efficiency >1,000 ppm and result in excessive sludge generation that translated into unplanned downtime and maintenance. The chemical coagulation results in a costly and labor-intensive operation that was sending ~$2MM worth of copper to a landfill. They desired a solution to recover the value of the copper, reduce both planned and unplanned costs, and assured discharge compliance.
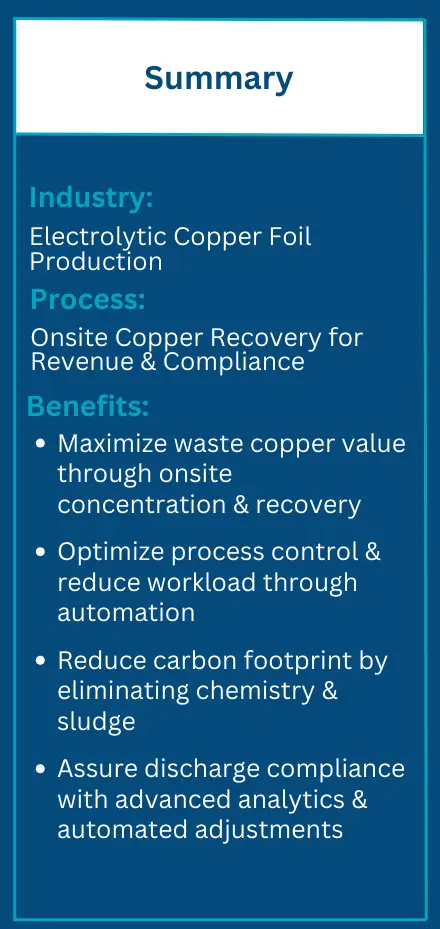
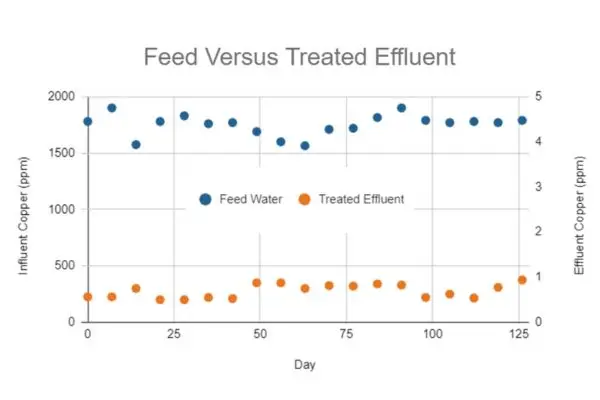
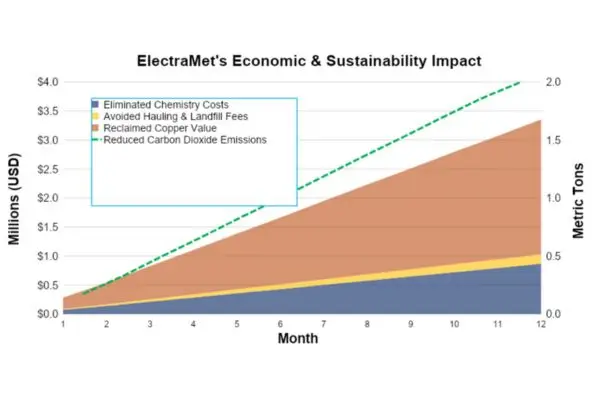
Proven Results | Case Study
The electrolytic spent bath and finished surface wastewater were mixed producing a final wastewater stream with ~1,800 mg/L Cu. Due to concentration & chemistry variations, the plant had difficulty attaining reliable environmental compliance. The permit limit for the facility was ~2 mg/L and the compliance team required a target effluent concentration of <1.0 ppm to reduce risk and enable countermeasures if needed.
The customer installed ElectraMet’s Alpha System (for discharge compliance) to replace the floc-reactor (chemical precipitation with a floc-tube dissolved air flotation system). The Alpha system has successfully and reliably achieved discharge compliance, maintaining <1.0 ppm [Cu]. Additionally, the system was able to recover the copper as high purity tubes (> 99.9%), yielding >$2,000,000 annually in previously unclaimed revenue. The Alpha System has established process control for environmental compliance while continuing to provide 99.9% removal of copper from the waste stream, demonstrating an unparalleled and unrivaled metal recovery solution.
ElectraMet’s automated electrochemical systems selectively remove and recover copper from complex process water or wastewater streams. The system is modular and can scale as production grows. The system consumes very little power (~0.12 kWh/m3 treated) while delivering a significant return on invested capital. ElectraMet’s onsite capture and recycling technology presents a circular and economical solution for handling copper in process/waste streams that translates into a competitive advantage for its customers. ElectraMet’s economic and environmental solution is a winning combination for plant leadership, its employees, its shareholders, and the surrounding community.
Additional observed benefits include:
(1) Eliminated > 3,000,000 pounds of sludge per year,
(2) Reduced operator labor for restorative maintenance by 100%,
(3) Analytics-informed troubleshooting maximized uptime and process awareness, and
(4) Increased personnel time spent on preventative maintenance for other systems by 22%.