Background
Printed circuit board (PCB) manufacturing utilizes specific materials, chemicals, and processes to achieve efficiency and repeatability. These processes include direct metallization, electrolytic plating, etching processes, desmear or etchback processes, immersion lines, and others, which can generate dissolved metals such as copper (Cu) in both process and waste streams. Traditional methods of copper recovery, such as electrowinning, are time, space, and energy-intensive and can produce waste or sludge. Electrowinning can effectively remove bulk copper down to around 3,000 mg/L (ppm), but it often requires special chemistry and heavy equipment to handle the large copper sheets weighing over 200 kg. Moreover, to meet compliance regulations, additional chemicals are necessary to remove the remaining copper for discharge, resulting in the generation of hazardous sludge, which incurs expensive handling and disposal costs.
Challenges
A PCB manufacturer faced challenges with rising costs for chemistry and sludge hauling, primarily due to unplanned price increases. Although the electrowinning process was effective in removing copper, it required expensive cathodes for copper plating and demanded extensive maintenance to sustain its functionality. Moreover, the site encountered difficulties in sourcing chemicals due to backorders. The facility was removing copper at a rate of 10.8 kg/hour, resulting in 64,800 kg/year with a cash-equivalent value of $498,960. The company considered involving a third-party to handle the copper-laden waste that couldn’t be extracted through electrowinning. However, they were offered minimal return for the copper value in the liquid waste. The company sought a comprehensive solution to maximize copper revenue, eliminate the challenges associated with chemicals and sludge, avoid costly maintenance for electrowinning, and alleviate the workload on their staff.
Summary
Industry:
Printed Circuit Boards.
Process:
Copper removal & recovery for revenue & compliance.
Benefits:
- Recover copper value without generating waste/sludge.
- Eliminate chemicals & ion-exchange headaches.
- Assured compliance with real-time feedback.
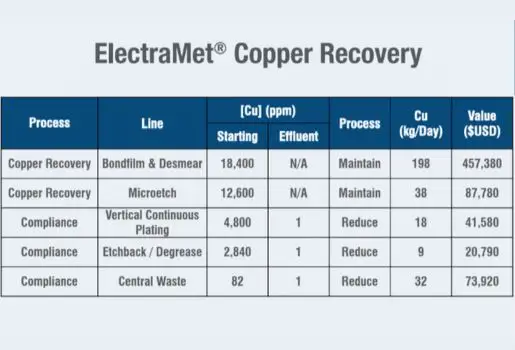
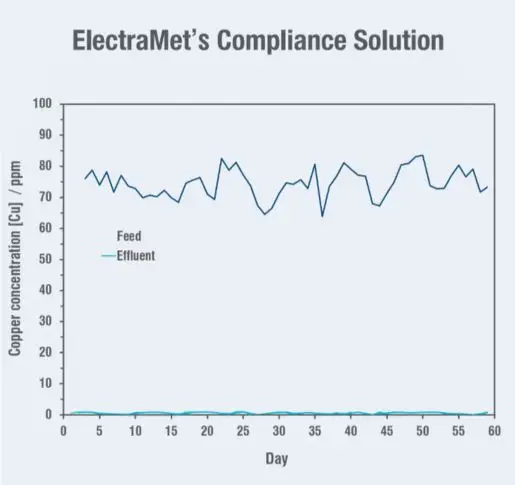
Proven Results | Case Study
The recirculating concentrated etchant loops with copper concentrations of up to 60,000 mg/L, the degrease and rinse line with copper concentrations of approximately 3,000 mg/L, and the dilute metals discharge streams with copper concentrations of around 80 mg/L posed challenges for reliable copper recovery and compliance in a PCB manufacturer. Process engineers had to ensure that the copper concentration in the recirculating loops remained within tight specifications (up to 60,000 mg/L), while the compliance team mandated a maximum of 1 ppm copper in the effluent discharge.
ElectraMet’s automated solution was implemented to achieve the following objectives:
(a) Replace the electrowinning solution to reduce energy consumption and eliminate the complexities associated with copper extraction.
(b) Replace chemical precipitation to maximize copper revenue and eliminate concerns related to chemical costs and sludge handling.
(c) Optimize the value of copper recovery.
Site expectations were met through the capture and recovery of all copper in the streams as 99.99% pure copper in approximately 10 kg copper tubes, simplifying the offloading process for staff.
ElectraMet’s automated electrochemical process selectively removes and recovers copper from complex process water or wastewater streams. The system is modular and can be scaled as production grows. It consumes minimal power, less than 0.12 kWh/m³ treated. With its capture and recycling technology, ElectraMet’s chemical-free process offers an economical and environmentally friendly solution for handling copper in process/waste streams. This combination of economic and environmental benefits is advantageous for the plant, its employees, and the surrounding community.
Additional observed benefits include:
- eliminated > 40,000 pounds of sludge,
- reduced operator hours due to automation,
- analytics-informed troubleshooting maximized uptime, and
- increased personnel time spent on preventative maintenance for other systems.